How to Optimize Your Supply Chain with an EMS Partner
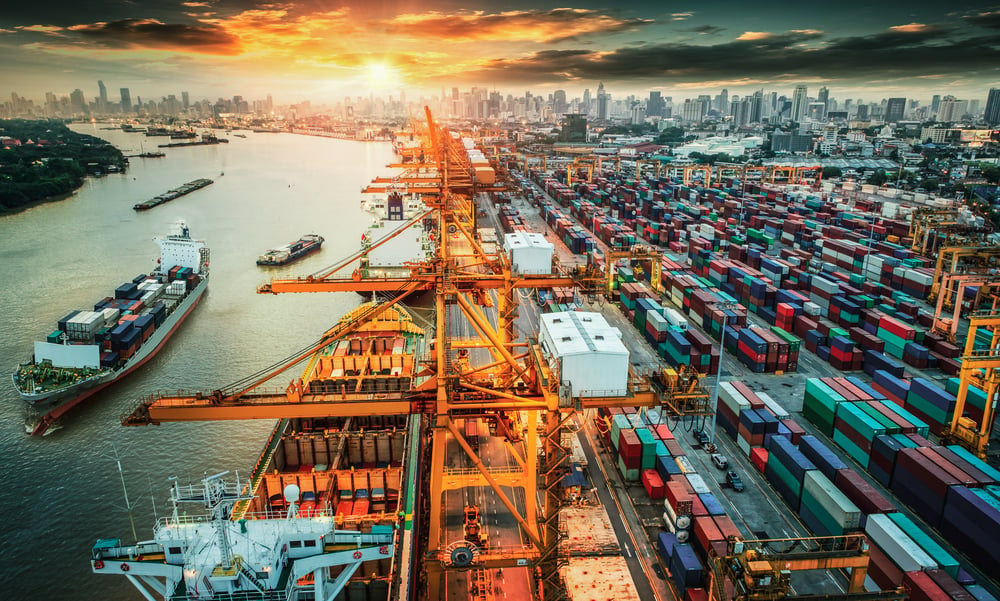
In today's globalized, fast-evolving market, OEMs confront unprecedented supply chain challenges. Rising material costs, geopolitical instabilities, and rapid technological shifts demand a balance of cost efficiency, risk management, and speed to market. Many OEMs turn to EMS providers, tapping their expertise and global networks as a lifeline. But success isn't automatic - it requires active collaboration. A strong OEM-EMS partnership is the key to optimizing your supply chain.
The Cost-Saving Potential of a Strong EMS Partnership
A strong EMS partnership can transform cost management. Benefits include:
- Optimized Bill of Materials (BOM) and Procurement Strategies: Streamlined sourcing lowers expenses.
- Supply Chain Visibility and Risk Mitigation: Transparency reduces surprises.
- Lean Manufacturing and Operational Efficiency: Waste reduction boosts margins.
- Scalability and Demand Forecasting: Flexible production meets market shifts.
- Design for Manufacturing (DFM) and Engineering Cost Avoidance: Smart design cuts rework.
- Post-Manufacturing Services and Lifecycle Cost Reduction: Long-term savings emerge.
The right EMS provider turns these opportunities into measurable gains. Not all excel equally - choose one with proven cost control to cut total landed costs and lift profitability.
Structuring OEM-EMS Partnerships
To formalize success, contracts should establish clear lead times, build release sizes, and inventory responsibilities, providing the clarity needed for effective planning. Flexibility must be built in to accommodate volume shifts, ensure continuity, and schedule regular reviews. Defining ownership of excess stock, allowing for scaling with advance notice, and pre-negotiating crisis responses further strengthens the partnership. Monthly operational reviews and a structured escalation matrix help maintain alignment. Ultimately, shared goals and open communication transform EMS into a seamless and strategic partner.
Early OEM-EMS Supplier Collaboration
Lead Time
Designing in isolation leads to sourcing challenges and delays. Instead, integrating Design for Manufacturing (DFM) early can reduce lead times by 20-30% by aligning designs with available components and efficient production processes. New Product Introduction (NPI) planning with EMS expertise helps identify long-lead risks, such as chip shortages, upfront.
Cross-functional collaboration between engineers, procurement, and EMS partners streamlines design choices, replacing proprietary parts with readily available stock - cutting material costs by 5-10%. Holding weekly design reviews or co-locating OEM engineers at EMS facilities ensures real-world feasibility.
To enhance supply chain resilience, share preliminary demand plans early, allowing suppliers to prepare and secure long-lead components. Treat EMS as an innovation partner from the start to accelerate launch timelines and minimize redesign risks. Strong EMS-distribution partnerships play a critical role in ensuring smooth production and a faster time to market.
Cost
Build a robust supplier network. Rigorous qualification - assessing quality, stability, and capability - can trim procurement costs by 10-15% by eliminating risky vendors. Balance consolidation with diversification: focus spend on trusted suppliers for better pricing, while securing alternates to avoid single-source failures. For example, dual suppliers across regions can cut disruption risks and shipping costs. Qualify first, then trust - build a resilient, cost-efficient network upfront to support collaborative designs.
Visibility and Transparency Across the Supply Chain
Nearly half of businesses have limited visibility beyond their Tier-1 suppliers, yet greater transparency can reduce contingency costs by 10-15% through predictive planning. Integrating ERP systems, sharing forecasts, and using real-time dashboards improves accuracy and strengthens trust.
Establishing weekly status checks and clear escalation paths enhances supplier relationships and responsiveness. A collaborative, no surprises approach allows OEMs to react swiftly minimizing disruptions. Ultimately, visibility drives cost efficiency and service reliability by optimizing decisions across a well-qualified supply base.
Risk Diversification
Expect the unexpected. Multi-sourcing critical components cuts disruption risks by a third—think dual factories or backup chip suppliers. Pair this with contingency plans: safety stock for long-lead parts, rapid-response teams, and nearshoring to avoid tariffs. Split production across regions to shorten lead times and buffer overseas uncertainties. Diversify suppliers, plan ahead, and collaborate on “what-if” scenarios—your supply chain stays agile, ensuring continuity no matter the crisis.
Value Analysis and Value Engineering (VAVE)
Keep improving post-launch. VAVE teams analyze BOMs and processes, cutting costs 15-20%—think merging boards or swapping out over-spec’d parts. Ongoing EMS collaboration, with gain-sharing incentives, drives 8-12% extra savings. Periodic business reviews and cost planning ensure gains compound over time. Relentlessly ask: “Are we getting the best value?”—VAVE keeps products competitive across their lifecycle, building on higher supply chain resilience.
Outsourcing thrives on partnership. Rigorous supplier vetting, real-time visibility, diversified risks, early collaboration, and continuous improvement—these strategies drive higher supply chain resilience. By qualifying suppliers and sharing data, OEMs can navigate blind spots. Diversified plans and early EMS input slash lead times. Continuous VAVE keeps costs competitive. Strong contracts align EMS incentives with OEM goals. The global market won’t ease up, but an optimized supply chain turns challenges into advantages. Partner with EMS, collaborate, and drive continuous improvement.
The evolving challenges of the global market won’t disappear, but with the right approach, OEMs can turn their supply chain into a competitive advantage, rather than a vulnerability. An optimized supply chain – one that is cost-competitive, resilient to volatility, and quick to respond – enables your business to deliver for customers no matter what the world throws at you.
Sources
- Deloitte. (2024). Supply Chain Digital Transformation Report
- Fictiv. (2023). 2023 State of Manufacturing Report
- KPMG. (2024). Global Supply Chain Resilience Survey
- Omdia. (2023). Semiconductor Market Forecast 2023-2027
- Supply Chain Drive. (2025). 2025 EMS Industry Trends Outlook
- ZVEI - German Electrical and Electronic Manufacturers' Association. (2014, updated 2024). Guideline: Supply Chain Management in Electronics Manufacturing
- Mastering Supply Chain Strategies: Insights from Industry Leaders
- Enhancing Supply Chain Transparency and Cost Management in Electronic Manufacturing Services
- Industry insights from anonymized case studies and expert interviews (2024).
Join Our Subscribers
You May Also Like
These Related Stories
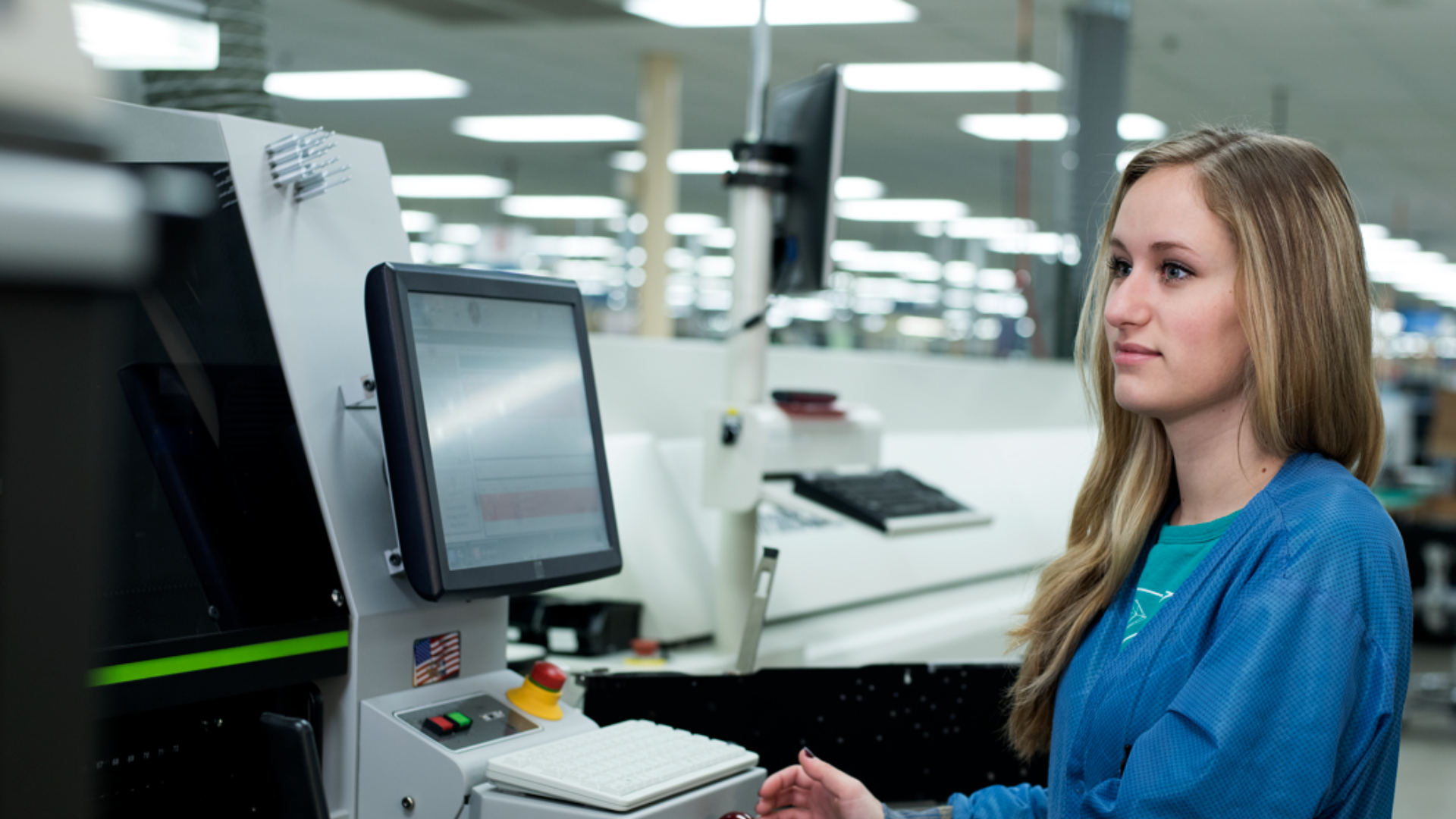
Tariffs, Reshoring, and Supply Chain Strategies in the EMS Industry
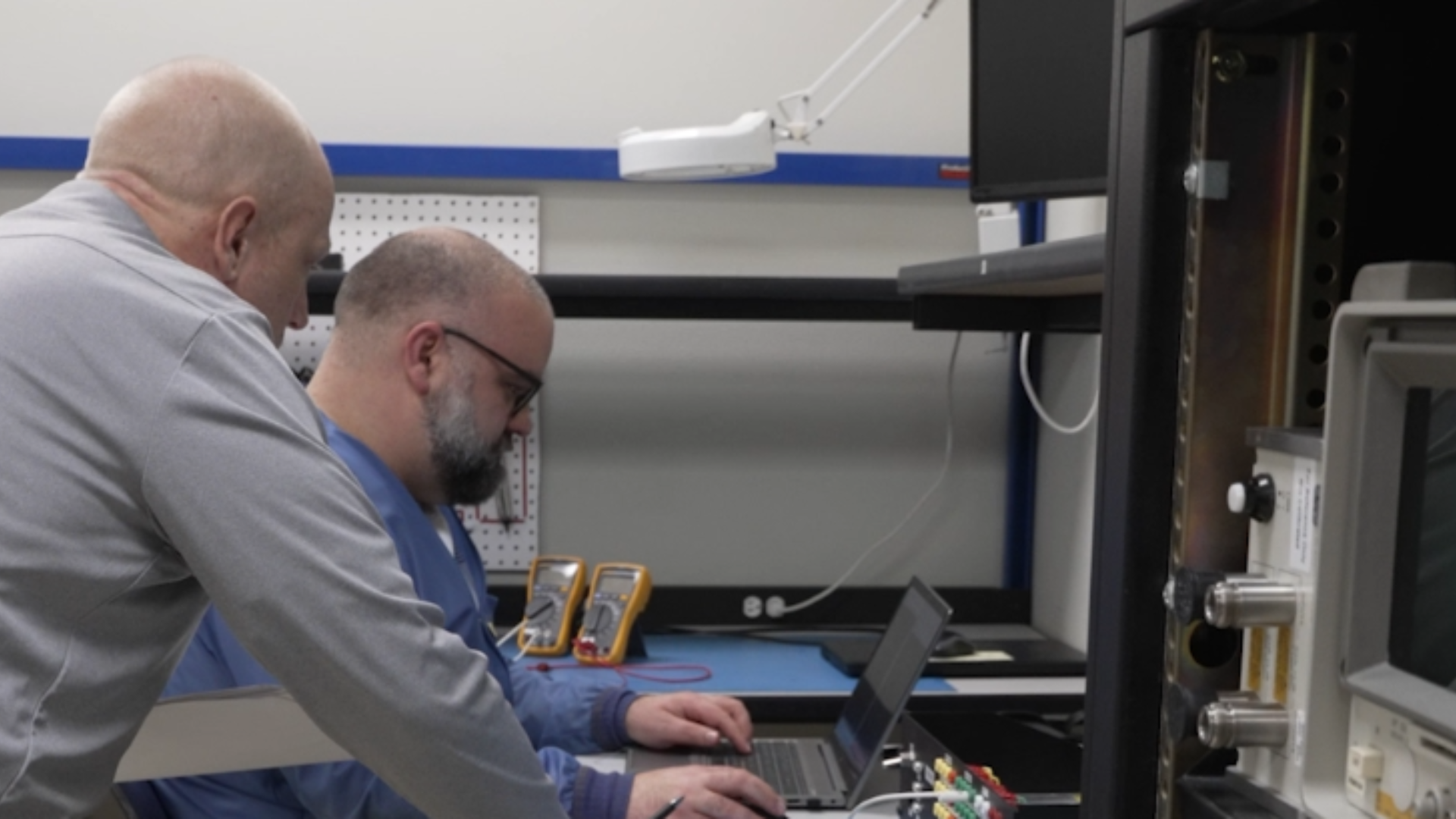
Why You Should Outsource Electronic Design
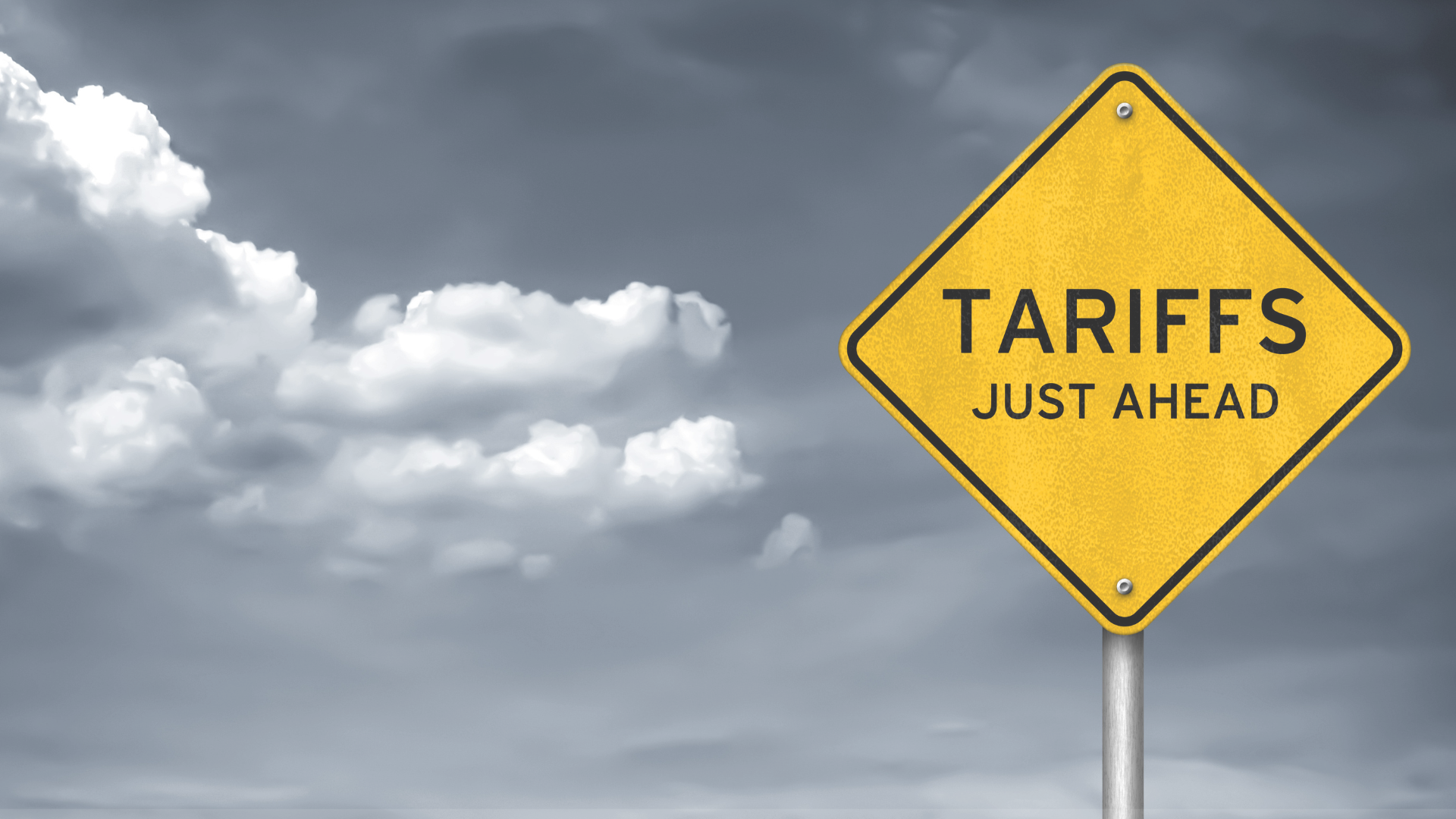