Tariffs, Reshoring, and Supply Chain Strategies in the EMS Industry
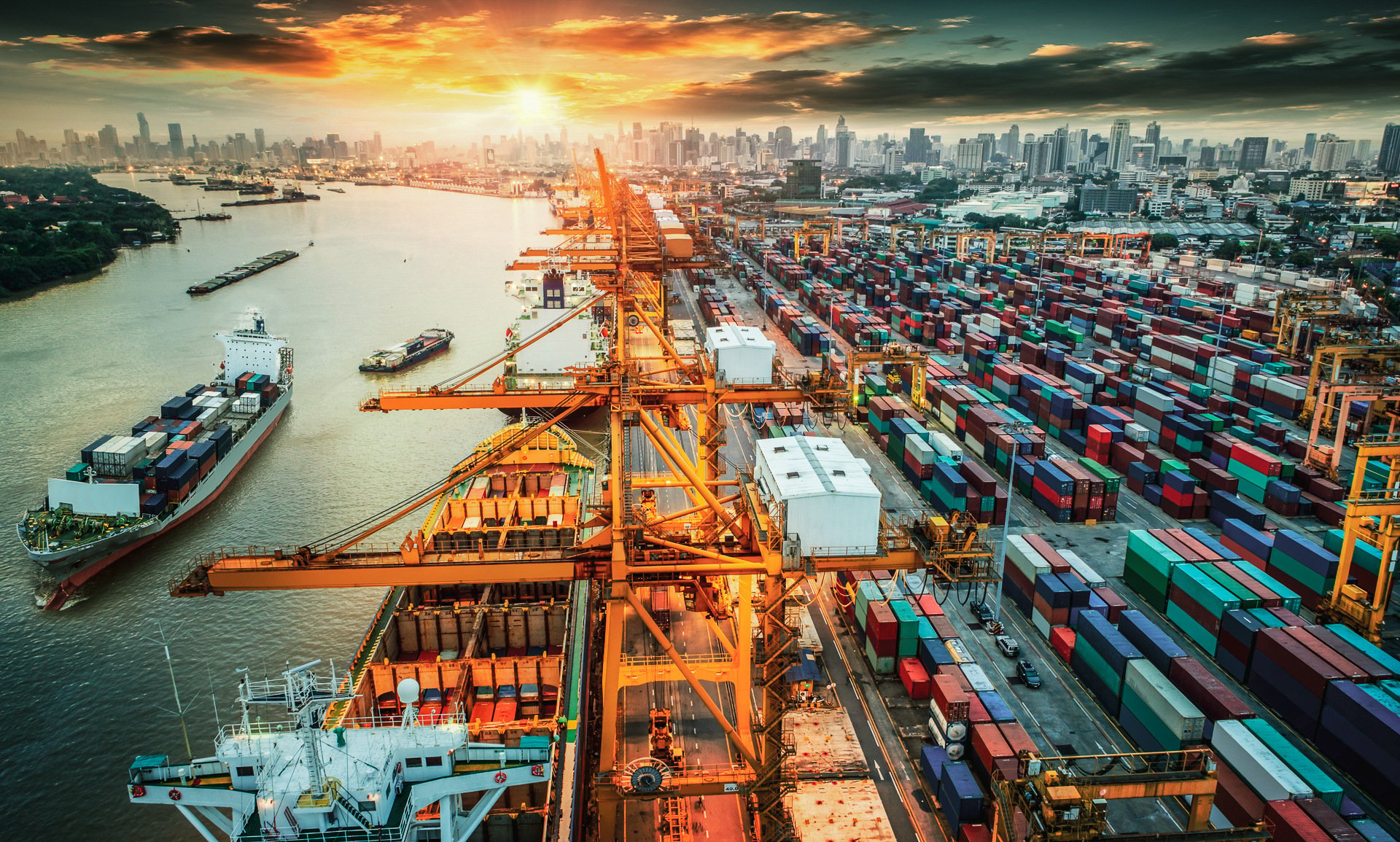
The global electronics manufacturing services (EMS) industry faces a rapidly shifting trade environment in 2025. U.S. tariffs on electronics – including Section 301 tariffs on Chinese imports – have transformed cost structures and sourcing strategies for components like printed circuit boards (PCBs) and semiconductors. At the same time, manufacturers are embracing reshoring—bringing production back to the U.S.—and nearshoring to countries like Mexico, driven by government incentives (such as the CHIPS Act) and recent supply chain disruptions. This white paper explores how tariffs on electronics, reshoring trends, and innovative supply chain strategies are reshaping the EMS landscape. We analyze their impact on OEMs and EMS providers, highlight actionable cost mitigation tactics, and put the geopolitical forces in context with insights from experts and 2025 policy updates.
U.S. Tariffs on Electronics in 2025
China Section 301 Tariffs 2025: Ongoing and New Measures
The U.S. has maintained broad tariffs on Chinese electronics imports since 2018 under Section 301 trade actions. Hundreds of billions of dollars in goods have faced duties – typically a 25% rate on electronics-related imports from China. For example, many electronic components and PCB assemblies from China have been subject to a 25% tariff since 2019 (after initially being 10% in 2018). These tariffs remain largely in place: a 2024 Biden Administration review chose to retain existing 301 duties on most Chinese goods while even expanding tariffs on strategic high-tech items. Notably, new measures will raise duties up to 25–50% on certain semiconductor products starting in 2025 to complement domestic chip investments. This underscores the continued focus on electronics in U.S. trade policy.
2025 Update: In February 2025, the U.S. Trade Representative (USTR) introduced a new tranche of Section 301 tariffs, raising duties to 35% on select Chinese-made microcontrollers and memory chips critical for automotive and IoT applications. This escalation, announced February 15, 2025, aims to further incentivize reshoring of these supply chains – though industry groups warn of potential short-term shortages given limited U.S. capacity.
Tariffs on PCBs: Printed circuit boards – critical substrates for electronics – have been a focal point of U.S. trade action. Currently, imported PCBs from China carry a 25% tariff, but there are important exclusions. Since 2019, the USTR has periodically excluded two-layer and four-layer PCBs from these tariffs due to limited domestic capacity. Those exclusions have been renewed multiple times and are now extended through May 31, 2025, meaning 2-layer and 4-layer bare boards from China can enter tariff-free until that date. Other PCB types (e.g. multi-layer boards above four layers) still incur the 25% duty. This policy attempts to shield simpler PCB imports from extra costs (to avoid supply shortages) while pressuring China on more advanced boards.
Tariffs on Electronic Components: Beyond PCBs, numerous electronic parts are on the tariff lists. Section 301 actions included a wide range of components (semiconductors, capacitors, connectors, etc.) used by OEMs and EMS firms. Initially, about $200 billion in goods at 25% tariffs encompassed many consumer electronics and parts. In 2024, USTR specifically targeted strategic electronics inputs – proposing tariffs up to 50% on certain semiconductors and even considering 50% duties on silicon wafers where China dominates. By late 2024, expanded tariffs (25%–100% rates) were approved on roughly $18 billion worth of tech-related imports such as chips, batteries, and medical electronics. These moves show that trade policy is not only maintaining earlier tariffs but also zeroing in on electronics deemed vital for national security and supply chain resilience.
2025 Update: On March 1, 2025, USTR confirmed a 75% tariff on Chinese lithium-ion battery cells for electric vehicles (EVs), effective April 2025, citing concerns over China’s dominance in EV supply chains. This move complements the Inflation Reduction Act’s push for domestic battery production, although EMS providers note it may raise costs for EV-related electronics in the near term.
Other Trade Measures: Section 232 metal tariffs (25% on steel, 10% on aluminum) also indirectly affect the EMS industry supply chain. Aluminum enclosures or steel chassis parts face higher costs unless exempted (Canada and Mexico, for instance, are exempt under quotas). Additionally, U.S. tariffs on certain Chinese finished goods (like some consumer electronics) can impact demand and influence production location decisions for EMS providers. In summary, as of early 2025 the tariff landscape for electronics is characterized by sustained import taxes on Chinese-sourced components and boards, with targeted increases on high-tech items but also selective relief (exclusions) where no easy alternatives exist.
Tariff Impact on EMS Providers and OEMs
Tariffs can impose significant cost increases and operational challenges for both original equipment manufacturers (OEMs) and EMS companies. A 25% tariff on essential inputs directly raises the bill of materials cost for electronics producers, squeezing profit margins unless those costs can be passed on. Many manufacturers have indeed faced higher production costs as importing components from China now carries hefty duties. These added costs often cascade down to consumers – for instance, one computer OEM (Acer Inc.) announced roughly a 10% price increase on laptops to offset U.S. tariffs. Thus, tariffs contribute to higher end-product prices, feeding into inflationary pressures in electronics markets. Beyond cost, supply chain disruptions have been a major side effect. The sudden imposition of tariffs forced companies to reconfigure supply lines and adjust logistics. Some OEMs pulled in extra shipments before tariff deadlines and then had to navigate new customs procedures and reroute goods afterwards.
EMS providers with global footprints saw customers shifting volume out of China to tariff-free locations, often on short notice. This created complexity and delays as companies adjusted to new suppliers or relocated assembly of products mid-stream. In some cases, critical component availability became an issue if alternative sources were limited outside the tariffed country. All of this has required greater supply chain agility from EMS firms.
EMS companies themselves have sometimes had to absorb tariffs or find creative workarounds. Many EMS contracts allow price adjustments for component cost changes, but not all adjustments fully cover the 25% hike – leading to tough negotiations between EMS providers and OEM customers. Some EMS providers reported narrower margins on projects heavily reliant on Chinese parts until sourcing could be diversified. Others responded by shifting production geographically. For example, an EMS might move an assembly line for U.S. customers from its China plant to a Mexico facility to eliminate the tariff, even if it meant duplicating tooling or retraining staff. These strategic moves incur short-term costs but were necessary to minimize long-term tariff exposure for both EMS companies and their OEM clients.
Moreover, tariffs have pushed companies to rethink inventory strategies. Faced with cost uncertainty, about one-third of manufacturers adjusted inventory – either by pulling in shipments early or stockpiling components before tariffs hit. While some increased inventories to hedge against future tariff hikes, others reduced orders when end demand weakened due to higher prices. Such shifts can distort normal demand signals, adding to the supply–demand mismatch issues that often plague electronics (e.g. the bullwhip effect).
In summary, U.S. tariffs have raised production costs, spurred price increases, and forced supply chain realignments in the EMS industry. OEMs and EMS providers that rely on Chinese sourcing have faced difficult choices: absorb the cost (hurting margins), pass it on (risking sales), or invest in rerouting their supply chains. The net effect has been a more complex cost structure and a greater need for strategic flexibility. Industry surveys confirm that trade policy is a top concern for electronics manufacturers. On the positive side, tariffs have also made domestically produced or non-Chinese components more price-competitive, creating opportunities for suppliers in regions like North America that were previously undercut by cheaper Chinese parts. This dynamic is one reason tariffs are often intended to encourage local sourcing – though in practice the adjustment period has been challenging for many firms.
Reshoring Electronics Production: Trends and Investments
One notable outcome of recent trade disruptions is a wave of reshoring (and nearshoring) in the electronics industry. Faced with tariffs and pandemic-era supply shocks, companies have been re-evaluating the risks of far-flung supply chains. Many are choosing to bring manufacturing closer to end markets, especially in critical technology sectors. According to the Reshoring Initiative, U.S. companies announced 287,000 jobs in 2023 from reshoring and foreign direct investment – the second-highest year on record. This continues an upward trend that accelerated in 2021–2022. Electronics and electrical products (notably semiconductor fabs and EV battery plants) have been a huge driver, accounting for roughly 39% of announced reshoring jobs in 2023. Government incentives like the 2022 CHIPS Act (for semiconductors) and the Inflation Reduction Act (for EV supply chains) have undoubtedly fueled this growth.
2025 Update: In January 2025, the U.S. Department of Commerce announced $2 billion in new CHIPS Act grants to support smaller PCB and component manufacturers, aiming to close gaps in domestic supply chains by mid-2026. Early recipients include a Texas-based EMS firm expanding its multilayer PCB capacity.
Major investments are also underway in U.S. electronics manufacturing. For example, TSMC’s $40 billion semiconductor fab in Arizona and Intel’s expansions in Arizona and Ohio represent efforts to reestablish domestic chip production capacity and reduce reliance on Asian foundries. In the PCB and assembly arena, some OEMs have built new U.S. facilities. A case in point is Schweitzer Engineering Laboratories (SEL), which in 2023 opened a $100 million PCB factory in Idaho to supply its own electronics. By producing PCBs in-house, SEL improved its supply chain resiliency and dramatically cut lead times (going from design to a tested board in days). The facility, one of the largest PCB plants in the U.S., was fully funded by SEL and is expected to pay for itself within 2–3 years – a striking example that domestic production can be cost-competitive for specialized needs. Such success stories are encouraging other companies to consider U.S. fabrication for critical components.
Drivers of Reshoring
Several factors are driving this reshoring/nearshoring movement. Tariffs on Chinese imports make U.S. or regional production financially more viable in many cases – avoiding a 25% import duty can offset much of the higher labor or overhead cost of domestic manufacturing. Supply chain resiliency is another motivator: the COVID-19 pandemic and geopolitical conflicts exposed the risks of over-reliance on distant suppliers. Shorter supply chains (e.g. manufacturing in the U.S. or Mexico) mean less transit time, more control, and less vulnerability to global transport disruptions. National security and IP protection concerns also encourage domestic production for sensitive electronics (defense, telecom infrastructure, etc.), a point reinforced by government policies that favor U.S.-made electronics in federal contracts. Additionally, various government incentives – beyond the CHIPS Act – offer tax breaks, grants, and credits to manufacturers investing in U.S. facilities (ranging from R&D tax credits to subsidies for semiconductor fabs and battery plants).
Challenges in Reshoring Electronics Production
Despite this momentum, the reshoring renaissance is not without challenges. Companies often encounter higher labor and operating costs in the U.S., and workforce shortages in manufacturing roles are acute. About half of U.S. manufacturing job openings for skilled workers remain unfilled due to a skills gap. Even when firms build new factories, finding enough trained technicians and engineers can be difficult. Training programs and apprenticeship pipelines need to scale up to support the influx of manufacturing jobs. Another challenge is that the supply chain infrastructure for electronics (suppliers of components, raw materials, chemicals, etc.) has largely migrated to Asia over decades. Rebuilding that ecosystem domestically will take time and significant investment. This is evident in semiconductor reshoring: fabs are coming, but packaging and materials suppliers must follow to complete the value chain.
Even so, the current trajectory suggests a continued “rebalancing” of electronics manufacturing. Not all production will return – cost-sensitive, labor-intensive assembly will still occur in low-cost regions for many consumer devices. But for high-value or high-risk products (chips, PCBs for critical systems, EV components, aerospace electronics), we can expect more capacity in the U.S. and allied countries. Notably, 2023’s reshoring job announcements nearly matched the record 2022 levels, indicating strong momentum supported by both economics and government policy. Companies that have reshored often report improved supply stability and faster time-to-market as key benefits, beyond just tariff avoidance.
Tariff Mitigation in Electronics: OEM Supply Chain Strategies
Manufacturers and EMS providers are employing a variety of strategies to soften the impact of tariffs and optimize their operations. These approaches range from reconfiguring sourcing to leveraging legal trade tools. Below are several key OEM supply chain strategies for effective tariff mitigation in electronics manufacturing:
Diversify and Audit the Supply Base
Over-reliance on one country or supplier exposes companies to tariff risk. Diversifying sourcing – both internationally and domestically – is a primary mitigation strategy. Firms are qualifying alternate suppliers in tariff-free countries and conducting thorough supplier audits to ensure quality and reliability. For example, when U.S. tariffs hit Chinese PCBs, some manufacturers audited PCB factories in Thailand and found them capable and cost-competitive, enabling a shift of orders out of China. By multi-sourcing critical components from different regions, companies create a buffer against tariff-driven price spikes or import bans. Regular supplier audits and quality checks are crucial when onboarding new sources, to maintain standards even as the supply chain widens.
Optimize Product Design and Classification (Tariff Engineering)
Some companies are redesigning products or altering their import configurations to qualify for lower tariff rates – a practice known as tariff engineering. This legal approach involves importing products in forms that incur less duty, then finishing or assembling them after entry. For instance, an electronics maker might import certain components separately rather than as a fully assembled unit if the separate parts fall under a lower-tariff category. By carefully classifying goods under the Harmonized Tariff Schedule or making minor modifications to fit a different category, companies can significantly cut duties. It requires close coordination between engineering, supply chain, and customs compliance teams. Importantly, tariff engineering must remain within legal bounds – components should not be imported with sham alterations solely to evade duty (as one automaker learned in a costly settlement over adding temporary seats to vehicles to avoid truck tariffs). Done properly, however, adjusting designs and import practices can yield substantial savings without changing the product’s functionality.
Leverage Free Trade Agreements (FTAs)
Free Trade Agreements can be powerful tools to eliminate or reduce tariffs. Companies are examining where they can source parts from FTA partner countries so that finished products enter the U.S. duty-free or at lower rates. For example, under the USMCA (United States–Mexico–Canada Agreement), many electronics that meet rules of origin can be traded among the U.S., Mexico, and Canada with zero tariffs. An OEM might shift component sourcing from China to Mexico, or perform final assembly in Mexico, to take advantage of USMCA and avoid Section 301 tariffs. Beyond USMCA, the U.S. has FTAs with countries like South Korea, Singapore, and several in Latin America – all of which present alternatives for procurement or production. The key is to review existing FTAs and adjust supply chains to utilize them. This may involve qualifying new suppliers in those countries or relocating certain manufacturing processes. Over time, as global trade alliances evolve (e.g. potential Indo-Pacific agreements), staying agile in sourcing will let businesses tap into new tariff-free networks.
Utilize Foreign Trade Zones (FTZs) and Bonded Warehouses
Many companies are turning to foreign trade zones as a buffer against tariffs. An FTZ is a secured, designated location in the U.S. considered outside of U.S. customs territory for tariff purposes. Goods can be imported into an FTZ without paying duties upfront and can be stored, processed, or even assembled there. Tariffs are only due if and when the goods leave the zone into U.S. commerce – if they are re-exported or scrapped, no U.S. tariffs apply. This provides flexibility in managing tariff costs. For EMS providers, using an FTZ can mean importing components, assembling products in the zone, and then re-exporting finished electronics without ever incurring import tariffs (useful for global production hubs). Even if finished goods are sold in the U.S., companies can sometimes benefit from inverted tariffs – if the duty rate on the finished product is lower than the rate on its components, doing final assembly in an FTZ allows the lower rate to apply. Setting up FTZ operations involves administrative overhead and compliance management, but it’s a well-established mechanism to defer or reduce duty payments. Many large electronics firms operate FTZs or bonded warehouses to optimize cash flow and avoid “paying tariffs on inventory” that might later be re-exported or used for service parts.
Leverage Duty Drawback Programs
For companies that export a portion of their products, duty drawback is a valuable but sometimes underutilized tool. U.S. customs regulations allow a refund of up to 99% of tariffs and import fees paid on goods that are later re-exported or destroyed. In the EMS context, if imported components with tariffs are used to build a product that is then shipped abroad (for example, an EMS builds units in the U.S. and sends them to overseas markets), the company can claim back most of the tariffs originally paid on those components. Implementing a drawback program requires careful tracking of inputs and outputs and documentation to file claims. However, it can recoup substantial costs. Any firm engaged in global supply networks should evaluate its eligibility for drawbacks – this essentially neutralizes the tariff for any imported content that isn’t ultimately consumed in the U.S. Properly managing a drawback program (or partnering with specialists) can turn tariffs into cash refunds, improving overall cost efficiency.
Invest in Automation and Process Improvement
To counteract higher labor or material costs associated with reshoring and tariffs, companies are investing in automation and advanced manufacturing technologies. Automation helps offset the cost differential of producing in a high-wage location by boosting productivity and reducing labor needs. Studies have found that deploying robotics and digital process controls can reduce operating costs by 25–50%, helping make U.S. production more competitive with low-cost countries. For example, an EMS provider that automates PCB assembly or uses autonomous material handling can significantly cut the unit labor cost, thereby absorbing some of the tariff impact. Automation also improves consistency and yield – valuable when qualifying new suppliers or ramping up local facilities. Additionally, AI-driven supply chain software is being used to optimize inventory and logistics in the face of tariffs. These tools enable dynamic re-planning of shipments (to avoid high-tariff routes), consolidation of loads to reduce costs, and real-time visibility into supply chain changes. In short, technology – from factory-floor automation to supply chain analytics – is a key enabler for tariff mitigation strategies, allowing companies to run leaner and react faster in a volatile trade environment.
Negotiate Cost Sharing and Contract Adjustments
Another practical step is working with suppliers and customers to share the burden of tariffs. Some EMS firms have added clauses in contracts that trigger pricing adjustments when tariffs above a threshold apply, splitting the cost increase between the EMS and the OEM client. Likewise, OEMs have asked component suppliers to consider absorbing a portion of tariff costs or to find cost savings elsewhere to offset them. Open communication in the supply chain is critical – for instance, renegotiating a long-term supply contract might secure a better base price to counteract a new 10% tariff. While no one likes to pay more, collaborative approaches (perhaps splitting the tariff cost) can maintain relationships and keep the end-product price within an acceptable range. Companies that plan for tariff contingencies in their contracts and purchase orders are better prepared to respond quickly when trade policies shift. This also ties into accurate customs compliance – ensuring the correct tariff classifications (HTS codes) are used can prevent overpaying duties by mistake. Regular audits of import entries and supplier-provided codes help catch errors or opportunities for reclassification, which in turn can save money or avoid penalties.
By employing a combination of these tactics, many electronics companies have managed to significantly mitigate the impact of tariffs on their operations. The optimal approach often involves a mix of immediate actions (e.g. using an FTZ or reclassifying a product) and longer-term strategic shifts (e.g. moving production or investing in automation). Each company’s best solution will differ based on its product mix, supply chain footprint, and customer requirements, but the overarching theme is building flexibility into the supply chain. Tariffs and trade barriers can change with geopolitical winds, so a resilient EMS supply chain is one that can adapt sourcing locations, tweak product design, and optimize import/export processes with relative ease. Firms that develop these capabilities are better positioned to weather not only tariffs but other disruptions as well.
Geopolitical and Economic Drivers of Trade Policy Changes
Understanding why these tariff and reshoring dynamics are occurring requires a look at the broader geopolitical and economic picture. In recent years, tensions have risen between major trading powers – most notably between the U.S. and China. The tariffs on Chinese electronics were originally imposed due to concerns about unfair trade practices and intellectual property theft. They have since evolved into part of a broader strategy of “strategic decoupling” – reducing dependence on China for critical tech supply chains out of national security worries. Industry experts note that semiconductors and related components have essentially become a new front in great-power competition, with tariffs, export controls, and subsidies all being used to secure supply and technological advantage. For instance, USTR explicitly stated that raising tariffs on certain semiconductors to 50% was aimed at complementing U.S. CHIPS Act investments and countering China’s dominance in that sector. This linkage of trade policy with industrial policy highlights how economics and security are now deeply intertwined in decision-making.
Additionally, the experience of the COVID-19 pandemic and other disruptions (like the 2021 Suez Canal blockage and various natural disasters) exposed how vulnerable globalized supply chains can be. This led to a reevaluation of the offshoring-heavy, just-in-time models that had prioritized cost above all else. Policymakers and businesses alike began emphasizing supply chain resilience and “de-risking.” Governments around the world – not just the U.S., but also in Europe and Asia – have introduced measures to onshore production of critical goods (from chips to pharmaceuticals) or at least to “friend-shore” them (source from allied countries). The tariffs and incentives in the U.S. are part of that trend, steering supply chains in what are perceived as more secure directions. For example, the U.S. has restricted exports of certain high-end chips to China and simultaneously used tariffs as leverage to push manufacturing to friendlier locations.
Economic factors also play a role. The long-term decline in U.S. manufacturing jobs created political pressure to protect domestic industries. Tariffs are a visible policy tool to demonstrate support for American factories and workers. However, economists often caution that tariffs can raise costs for downstream industries and consumers. Indeed, there is evidence that the China tariffs have increased input costs and contributed to inflation, while yielding less revenue than expected due to shifts in sourcing. Industry voices like IPC (a global electronics association) have lobbied against broad tariffs on components that the U.S. doesn’t produce in sufficient quantity (like many PCBs), arguing that these duties hurt American EMS firms more than they punish China. This debate continues in policy circles: how to balance the short-term pain versus the long-term goal of rebuilding domestic capacity.
Recent policy announcements reflect a mix of continuity and escalation. The Biden administration, despite initial expectations of a softer trade stance, has maintained most of the Trump-era tariffs and even expanded on them in targeted sectors. At the same time, the administration has engaged allies to form a more united front on supply chain security (for instance, coordinating with Japan and the Netherlands on semiconductor equipment export restrictions to China). On another front, new trade agreements have been sparse, but frameworks like the Indo-Pacific Economic Framework (IPEF) are being negotiated to set standards and possibly reroute trade flows among partner countries (though IPEF is not a traditional tariff-cutting FTA as of now). The global trade environment is thus in flux: old assumptions of ever-increasing free trade have given way to an era of managed trade, industrial policy, and selective decoupling in strategic industries.
Industry experts advise companies to stay alert to policy signals. For example, if political rhetoric suggests possible tariffs on other countries (there have been past threats of duties on Mexico or Europe for various reasons), contingency plans should be considered. The 2024 U.S. election cycle featured proposals for across-the-board tariffs on imports (e.g., a blanket 10% tariff on all imports was floated). While it’s uncertain such extreme measures would materialize, it underscores that trade policy is now a major topic in domestic politics. Similarly, tensions in East Asia – such as around Taiwan – could have profound effects on electronics supply chains and may prompt further U.S. trade actions or emergency measures. Global economic conditions also influence trade policy; high inflation might make governments more hesitant to add tariffs that raise consumer prices, whereas in a downturn, protectionist impulses could grow.
In summary, the push and pull of tariffs, reshoring, and supply chain shifts are rooted in geopolitical strategy (tech sovereignty, national security), economic nationalism (domestic job creation), and lessons learned from recent crises. The EMS industry sits at the intersection of these forces. By paying attention to expert insights and government announcements, companies can better anticipate changes. For instance, knowing that “tariffs are viewed as an easy political tool” despite their side effects can help firms lobby for smarter policies or prepare mitigation plans. Electronics executives are increasingly engaging with policymakers to convey how tariffs impact their businesses, contributing industry data to shape more targeted trade actions that achieve security aims without unnecessarily disrupting supply chains.
2025 Update: Post-2024 election, the incoming U.S. administration floated a proposal for a 10% universal import tariff in February 2025, which is still under debate as of March. If enacted, it could accelerate reshoring but also risks broader cost hikes across the economy.
Optimizing the EMS Supply Chain: Practical Steps Forward
Given the complex environment described above, what practical steps can electronics companies take to optimize their supply chains and thrive? Below is a consolidated checklist of actions and best practices derived from recent industry experience:
- Conduct a Tariff Exposure Audit: Map out your entire bill of materials and supply chain to identify which components or products are subject to tariffs and at what rates. This includes verifying the HTS classifications and country of origin for each item to ensure correct tariff treatment and avoid overpaying. An exposure audit helps prioritize mitigation efforts on the highest-impact areas.
- Develop a Sourcing Diversification Plan: Based on the audit, formulate a plan to qualify backup suppliers in low-tariff or tariff-exempt countries. Leverage resources like supplier databases and trade networks to find alternatives in regions such as Southeast Asia, Eastern Europe, Mexico, or domestically. Prioritize critical components (e.g. PCBAs, connectors, ICs) for second-sourcing. This plan should include timelines for testing and approving new sources, as well as dual-sourcing key items where feasible to reduce dependency.
- Leverage FTAs and Regional Agreements: Align your sourcing and production footprint to maximize the benefits of free trade agreements. For North American supply chains, ensure you meet USMCA rules of origin to trade tariff-free – this might involve sourcing a higher percentage of materials from within North America or adjusting your manufacturing bill of materials. Similarly, explore sourcing from countries with U.S. FTAs (South Korea, Australia, CAFTA-DR countries, etc.) for tariff-free entry. If your products can be partially produced in an FTA country, consider moving that portion of the process there.
- Implement Tariff Engineering Tactics (Legally): Work with your engineering and customs compliance teams to see if product modifications or kit assembly strategies could reduce tariff classifications. Even simple changes – like importing an unfinished assembly and doing final minor assembly in the U.S. – can sometimes reclassify the item to a lower-duty category. Be sure to document the business rationale and maintain compliance (the product as imported must genuinely meet the claimed classification). Use customs rulings or consult trade experts to guide these efforts. Over time, design new products with an eye toward tariff optimization (for example, selecting components or materials that don’t trigger high duties).
- Establish Foreign Trade Zone Operations: If you import significant volumes of components, consider setting up a Foreign Trade Zone for your U.S. manufacturing or distribution center. This allows you to defer paying tariffs until goods leave the zone, improving cash flow. More strategically, it enables tariff inversion – if your finished product would have a lower tariff rate than the imported parts, you pay only the lower rate. FTZs are especially useful if you re-export products, since you can avoid tariffs entirely on the re-exported portion. Weigh the administrative cost of FTZ management against the potential duty savings, which can be substantial for high-tariff items.
- Optimize Inventory and Shipping Schedules: Use strategic inventory planning to navigate tariff changes. If a known tariff increase is coming (or an exclusion is set to expire), it may make sense to pull in extra inventory before the effective date to buy time. Conversely, avoid over-stockpiling to the point of tying up excessive capital. Utilize bonded warehouses or FTZ storage for flexibility. Also consider shipping routes and intermediate stops – sometimes routing goods through certain countries can change the applicable tariffs (though rules of origin still apply). Work closely with freight forwarders and customs brokers to identify creative logistics solutions.
- Invest in Automation and Workforce Training: As you reshore production, invest in automation to keep costs competitive and meet throughput goals. Robotics, advanced pick-and-place machines, and process automation can significantly reduce labor content and improve quality, offsetting higher domestic wages and making localized manufacturing more viable. At the same time, invest in training your workforce on these advanced systems – a skilled workforce enhances productivity and can adapt to new processes or supply chain changes. Government grants or partnerships with local colleges (for apprenticeships) can support these training efforts and help close the skills gap that often accompanies reshoring.
- Enhance Supply Chain Visibility and Agility: In a world of rapidly shifting trade policies, having real-time visibility into your supply chain is crucial. Implement or upgrade supply chain management software to track shipments, lead times, and inventory across all tiers. This helps you react quickly if a tariff is suddenly imposed or if geopolitical events threaten a supplier. Scenario-planning tools can simulate the impact of events (like a 10% tariff increase or a port closure) and allow you to develop contingency actions. An agile supply chain – with options to reroute orders or switch sourcing on short notice – is a competitive advantage when dealing with trade uncertainty.
- Engage in Policy Dialogue and Stay Informed: Finally, actively monitor trade policy developments and engage with industry associations (e.g. IPC, NAM, SEMI) to stay ahead of changes. Submitting comments during USTR tariff review processes or supporting advocacy for tariff exclusions can influence outcomes. Stay informed through government notices, trade news sites (e.g. EMSNOW, Supply Chain Quarterly), and expert analysis so you can anticipate shifts. For instance, knowing that a key exclusion (like the PCB tariff exclusion) is set to expire in 2025 allows your company to lobby for an extension or prepare to adjust sourcing. Proactive engagement can sometimes secure relief – for example, many companies (through associations) successfully petitioned for reinstating certain tariff exclusions in 2022–2023. In short, treat trade policy as another business variable to manage, not a static background factor.
The EMS industry sits at the nexus of global trade and high-tech manufacturing, making it especially sensitive to tariffs and supply chain disruptions. Recent years have demonstrated both the vulnerabilities and the adaptability of this sector. U.S. tariffs on PCBs and electronic components have challenged companies to rethink their cost structures and logistics, but they have also catalyzed positive changes like diversifying supplier bases and boosting North American manufacturing. The concurrent reshoring trend – supported by strong economic and political tailwinds – is reshaping where and how electronics are made, with more investment flowing into U.S. factories and those of close trade partners.
For OEMs and EMS providers, navigating this landscape requires a strategic, proactive approach. Tariffs should be treated as manageable costs that can be engineered around through smart supply chain design, rather than as insurmountable obstacles. Companies that have implemented the strategies outlined – from alternate sourcing and tariff engineering to leveraging FTZs and new technologies – have found they can buffer much of the tariff impact and even turn supply chain resilience into a competitive advantage. Furthermore, aligning corporate strategy with the broader geopolitical reality (e.g. preparing for a decoupling of tech supply chains, or capitalizing on government incentives for local production) will position EMS firms and their customers for long-term success.
The geopolitical and economic forces driving trade policy remain complex and ever-evolving. Trade barriers might rise in some areas while free trade agreements expand in others. The prudent path for companies in the EMS industry is to remain agile: build flexibility into supply networks, maintain a globally aware perspective, and be ready to pivot as conditions change. In doing so, they can reduce risk and seize new opportunities – whether that’s winning business due to a reshoring initiative or avoiding a cost spike from the next round of tariffs. By combining up-to-date knowledge of trade policies with robust supply chain strategies, EMS providers and OEMs can weather the current tariff turbulence and emerge stronger and more resilient in the years ahead. Ultimately, a focus on tariff mitigation in electronics can turn a challenging trade environment into a catalyst for supply chain innovation and resilience.
Sources:
- Beauchamp, J. (2025, January 28). Fresh PCB Concepts: Tariffs and the Importance of a Diverse Supply Chain. I-Connect007
- GEODIS. (2024, September). Navigating Trade Uncertainty in 2025: Impact of Tariffs and Trade Policies.
- Pillsbury Trade & Sanctions Law. (2024, September 13). USTR Finalizes Section 301 Tariffs on Chinese Imports with Focus on Strategic Sectors.
- ACDi. (2025, February 28). How New Tariffs Could Reshape Electronics Manufacturing: The Case for Reshoring.
- Reshoring Initiative. (2024, July 12). Reshoring Creating Record Amount of Jobs (Material Handling & Logistics).
- Dahlgren, D. (2023, January 24). Taiwanese manufacturers to speed up investments in Mexico. Evertiq News.
- National Association of Manufacturers. (2023, August 11). A Homegrown Solution: SEL Makes Printed Circuit Boards.
- TrueCommerce. (2023, August 23). 8 Strategies to Mitigate New Trade Tariffs.
- Descartes. (2023). Import Tariff Mitigation Strategies.
- Sandler, Travis & Rosenberg. (2024, March 15). Tariff Engineering – $365M Settlement Highlights Need for Caution.
Join Our Subscribers
You May Also Like
These Related Stories
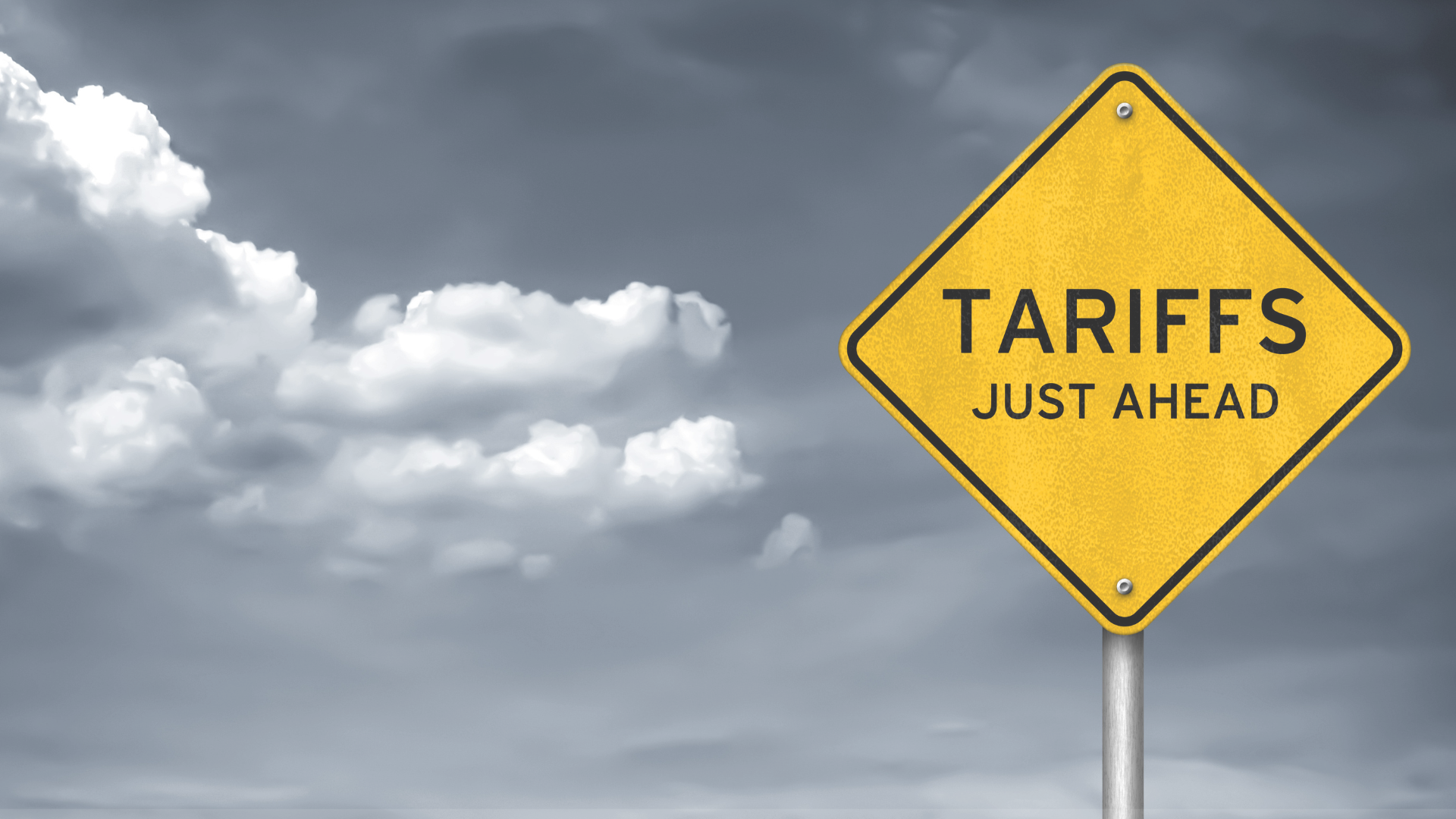
eBook: Tariffs, Reshoring, and the Future of Custom Electronics
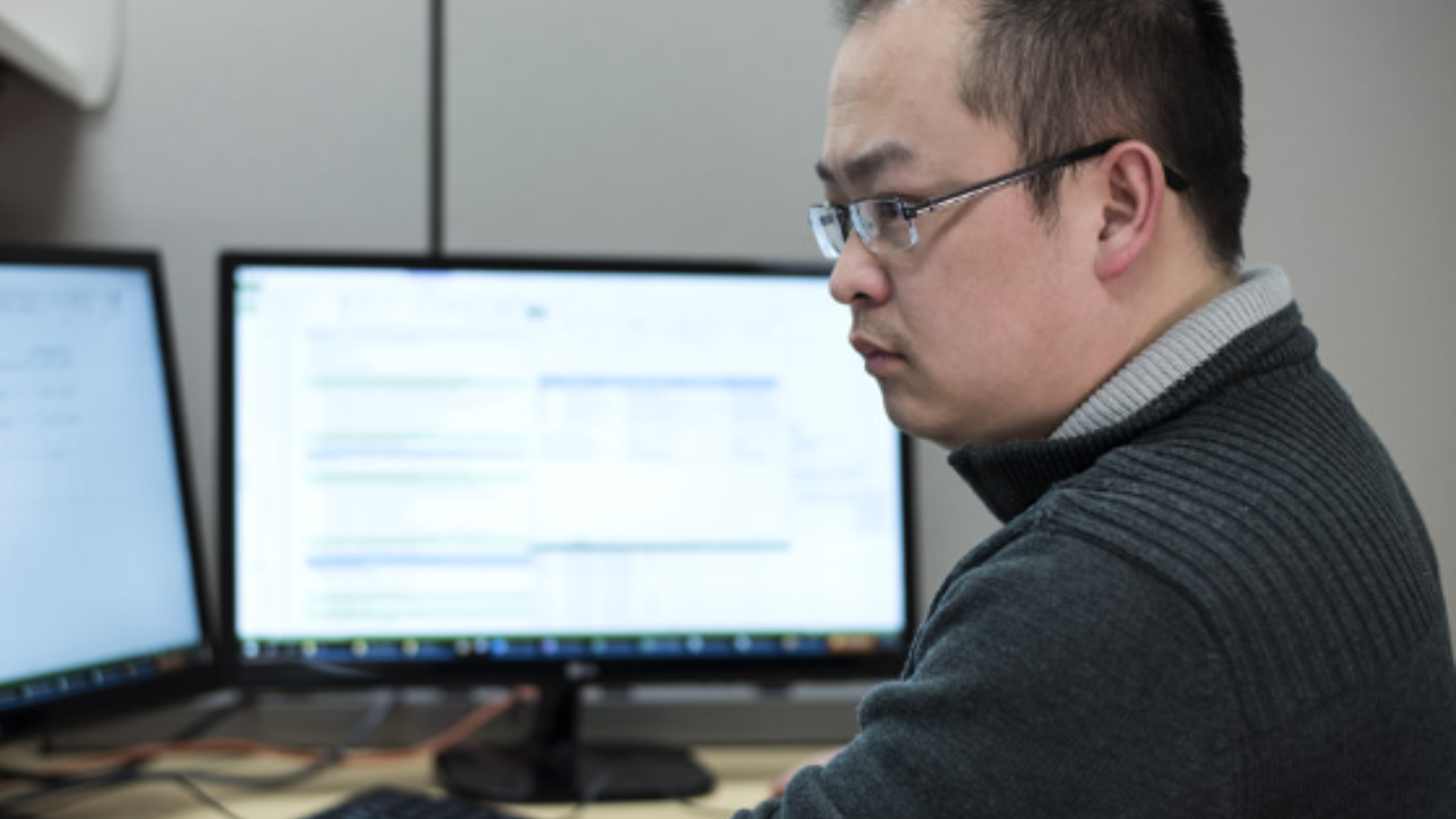
How to Optimize Your Supply Chain with an EMS Partner
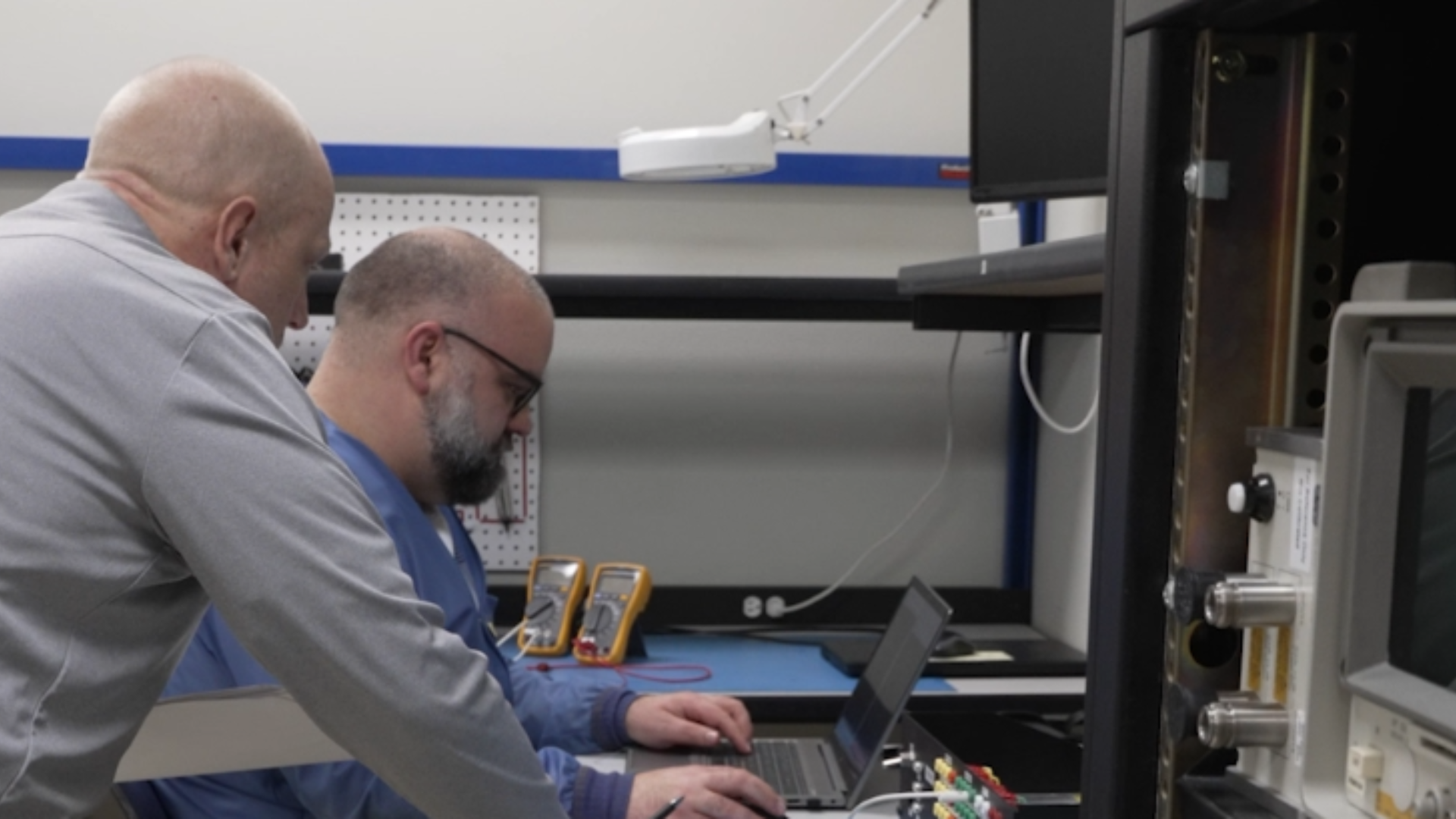