DFM - What Questions to Ask About Your Design
Why is DFM Important in the Manufacturing and SMT Process?
Design for Manufacturability (DFM) is the process of ensuring that quality, reliability, and cost-efficiency are optimized for a product before it's ever built. By incorporating DFM early in the design phase, you can avoid significant expenses and complications later in the product lifecycle.
Today's PCBA designs are increasingly complex, utilizing smaller components, higher component densities, and facing thermal challenges due to lead-free soldering requirements. This rising complexity can drive up costs and increase quality risks if not properly addressed during the design stage.
A comprehensive DFM review consists of two key components: automated Design Rule Checks (DRC) and manual evaluation by an experienced Subject Matter Expert (SME). While automated DRC can identify many potential issues, an SME can provide deeper insight and added value through their hands-on experience.
Engage with your assembler early in the process. They have a thorough understanding of their manufacturing environment and can offer a fresh perspective on potential solutions.
Why is Asking the Right Questions Early in the Design Phase Important?
Incorporating Design for Manufacturability (DFM) early in the design process is critical for maximizing efficiency, reducing board spins, and lowering overall costs. Asking the right questions upfront can help avoid costly rework later in the development cycle.
A helpful guideline to consider is the "Rule of 10": the cost to resolve a design issue increases tenfold with each subsequent phase of the product lifecycle. If a problem costs X to fix during the concept stage, it could cost 10X after prototyping, 100X after NPI and production, 1,000X once the product reaches the end customer.
Engaging with your assembler as early as the "back of a napkin" stage allows designers to more easily incorporate DFM feedback while critical elements - such as board size, form factor, component mix, and component technology - are still flexible. Once these factors are finalized, making changes becomes significantly more difficult. At that point, there may be broader implications to consider, including mechanical constraints, supply chain impacts, or compliance and regulatory certifications.
Why Does DFM Matter in Modern Manufacturing?
DFM is critical to success in modern manufacturing. With rapid advancements in today's electronics landscape, designers must be careful not to fall into the trap of adding unnecessary complexity without fully understanding the associated costs at the assembler or fabricator level. Just because something can be done doesn't necessarily mean it should be done.
To avoid surprises later in the process, reach out to your assembler early. They can help ensure that your design concepts are manufacturable at a reasonable cost - without introducing additional quality risks.
What Key Questions Are Important to Ask?
The key question to ask during the DFM process is, "What is the goal you're trying to achieve?" Evaluating a design solely from a cost perspective may introduce long-term reliability risks. Conversely, eliminating every potential reliability risk could result in significant budget impacts.
Striking the right balance is essential, and clearly understanding the design objective from the outset leads to a more effective DFM outcome. When reviewing any printed circuit assembly for manufacturability, consider the following general questions:
- What processes and how many will be required to build this product?
- Minimizing process steps will have a positive impact on overall complexity and cost.
- How will this product travel down the line and be presented to the manufacturing equipment?
- Will special processing and handling equipment be needed? Can the layout or panel design eliminate handling concerns?
- How will every component be placed and attached to the PCB?
- Will automation be possible or will there be manual operations?
- How will every component be reworked?
- Every manufacturing environment has some level of rework, is there a plan for every component?
- Is there a plan for field returns or upgrades?
- How will this product be tested?
- Is there access to in-process or end of line testing?
- How will field return testing be accomplished?
- How will this product be packaged and shipped?
- Is there an economical packaging solution to ensure the product arrives undamaged and in a presentable manner?
Answering these questions will reasonably assure that cost, quality, and throughput targets will be met, even before a single component is placed.
What Are Common Mistakes to Avoid in the DFM Process?
The biggest mistake you can make in the DFM process is skipping it altogether. This often happens due to tight release schedules, competing design priorities, a lack of understanding of assembly processes, and other constraints.
A robust DFM process requires a clear understanding of how the product will actually run through the factory - and within the limitations of the manufacturing environment where it will be built. To achieve this, partner with a supplier who can provide timely, practical feedback and who understands how your product will flow through their specific processes.
Engage your manufacturing partner early in the design cycle to fully realize the benefits of DFM and set your product up for long-term success.
Any activity used to transform individual components into a finished assembly is considered a process. Every process comes with its own set of requirements, and when those requirements are account for during the design phase, the result is a product that can be built more efficiently - with improved yield and throughput.
While DFM activities are most effective when initiated early in the design stage, they should continue throughout the entire product lifecycle. The best time to start thinking about DFM was yesterday - but if that didn't happen, now is the best time.
To learn more about SMT and our DFM services, click the link below.
Join Our Subscribers
You May Also Like
These Related Stories
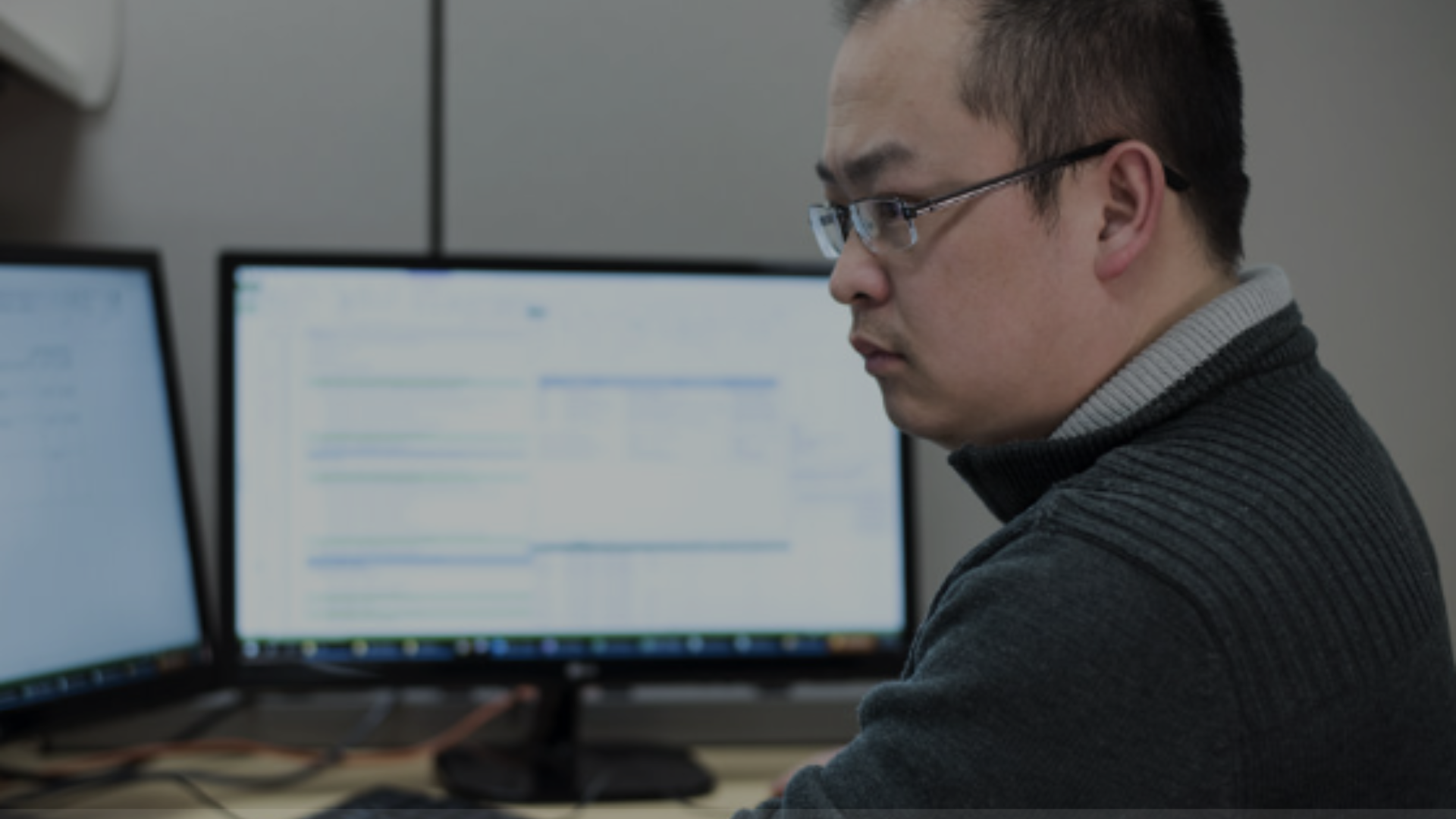
Project Management - Planning for Risk
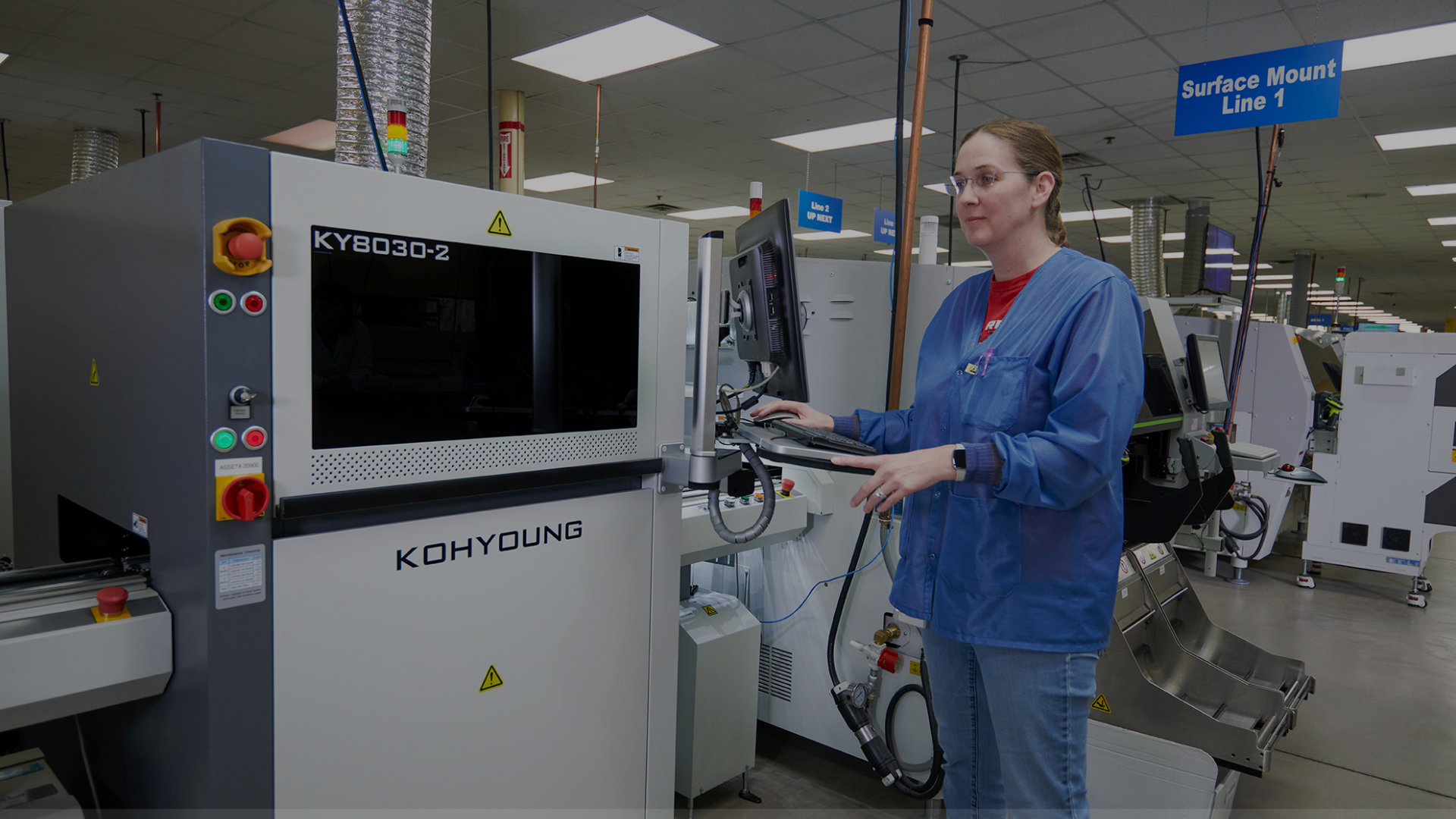
Everything Under One Roof - Design to Manufacturing
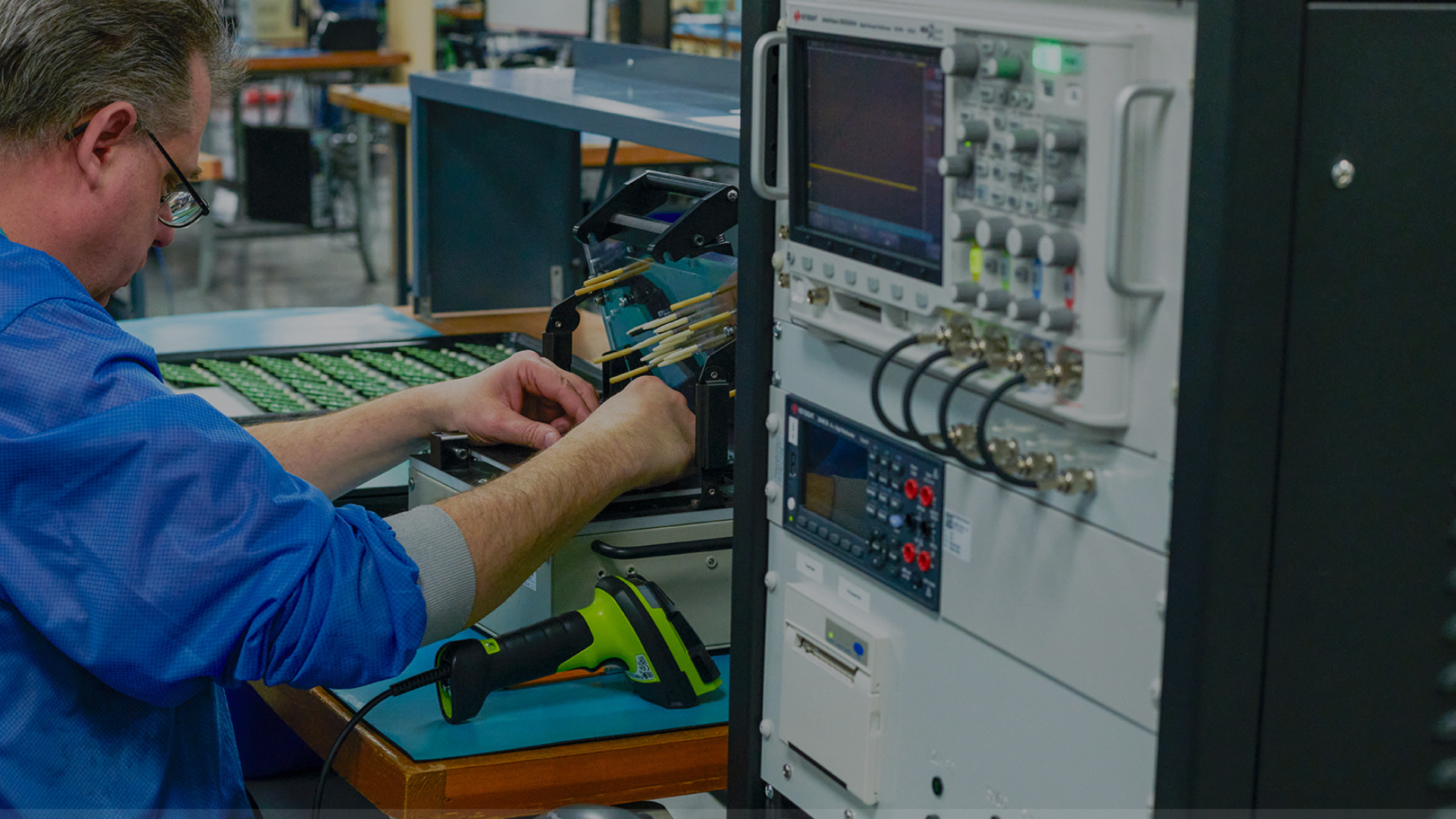